- Markets
- Catalog
- Services & Solutions
- Tools and Resources
- Downloads
- About Nexans
- Newsroom
-
Nexans Insights
- Nexans Insights
-
Blog Posts
- Overview
- The path to effective fire safety in buildings
- Big data & AI
- Electrical and Fire Safety
- IoT
- Unveiling innovations transforming the industry
- Transforming buildings industry with 3D printing and modular construction
- Powering the digital change
- Unleashing the power of DC buildings
- Sustainable buildings for a brighter future
- Industry 1, 2, 3, 4... and 5.0
- Nexans copper odyssey
- Localizador de tiendas
- Search
- Contact us
- Compare
- Sign in
Industry 1, 2, 3, 4... and 5.0
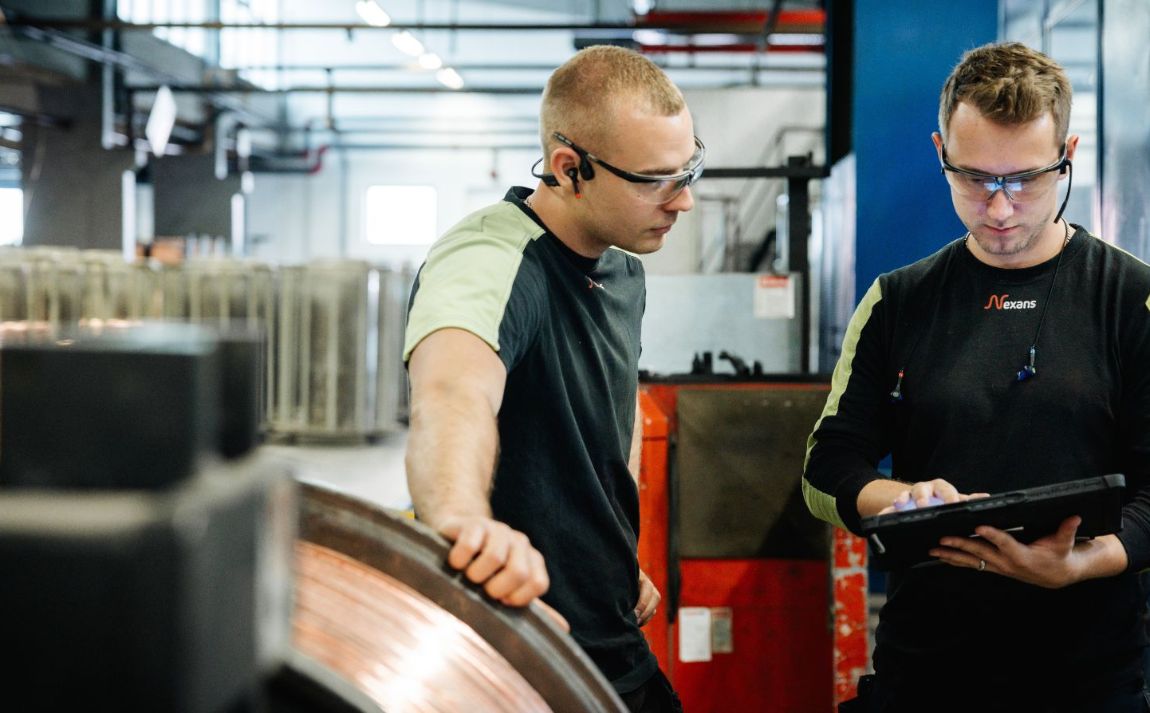
Nexans aligns its data with business operations
A shift is under way. Many countries, including the USA and France, are turning away from the factory-free economy – the dominant model of the past last 30 years – to rediscover the advantages of manufacturing at home. This shift creates a unique opportunity to promote the development of new-generation plants, reflecting new economic, social and environmental challenges. Local for local has always been the watchword at Nexans, which is seizing this opportunity to take a new step forward in its development. By integrating its rigorous management model with its international production base, the company will be in industry 4.0 mode by 2026.
When we talk about the digital revolution, we tend to think first of the glut of the information inundating our lives, every day of every week, announcing a new revolutionary smartphone, a new multi-cooker or the latest mind-boggling breakthroughs in artificial intelligence (AI). It’s a subject that has only recently come to the fore in the business world, with the fierce debate around the impact of AI on business activities and the rapid automation expected in many areas, from programming to accounting, medicine and law.
Paradoxically, industry has attracted far less interest as a subject of discussion. And yet it is a subject of key importance, not only in terms of jobs, innovation and value creation, but also in terms of sovereignty. The Covid-19 pandemic was a wake-up call for European countries, which became aware of the scale of their economic and strategic dependence, in the light of the tensions between China and the United States. Factories have a key role to play in adapting our economies to the new technological order.
How industry is reinventing itself with industry 4.0
This comes as no surprise, since changes in the workshops have always been associated with breakthroughs in technology, continuing a cycle that began with two industrial revolutions. The steam engine and the first factories were followed by the arrival of electricity, machine tools and mass production, and then – in the 1950s – by electronics, automation through programming, numerical control machinery, industrial robots and the first supervisory software packages.
The fourth revolution, currently unfolding, directly continues the ongoing process of computerization, while taking it to a whole new level. The first step is to establish a new energy base, moving away from the fossil fuels that powered the previous three revolutions. The second step is to maximize the use of a key new resource – corporate data – by building on a powerful high-tech mix that has now reached maturity: very high-speed infrastructure (fiber for fixed connections and 5G for mobile), combined with data hosting and mass processing (Cloud, Big Data, AI), decentralized intelligence and smart objects (IoT) and new forms of human-machine interaction (mixed reality, digital twinning, avatars).
This avalanche of innovations is paving the way for a complete rethink of the way companies work, with particular emphasis on all the processes involved in production. For many industrial powers, this is now a priority. It is no coincidence that Germany was the first to launch an Industry 4.0 plan in 2011, with an eye to maintaining the excellence of its industrial base. Pursuing the same objective, China is investing in high value-added factories in order to retain its industrial might and address a growing labor shortage. France adopted a similar strategy in 2015, with its Alliance for the Industry of the Future, an association of 32,000 companies meeting every year at the Global Industry trade show. This year, Nexans was in the spotlight, claiming two Golden Tech awards in the Designer and Maker categories at the 2023 event, held last March in Lyon.
Nexans 4.0 on course for 2025
These goals are part of a new commitment involving everybody at Nexans. The Group is moving towards the global digital integration of all areas of the company and its ecosystem in order to simplify processes, improve performance and response, boost productivity and safety, limit unnecessary operations, as well as to anticipate and plan for events (predictive maintenance, inventory management, customer satisfaction, etc.).
In a recent survey of French business, 98% of the companies interviewed said that they have already planned or deployed initiatives relating to Industry 4.0 (7th edition of the Wavestone barometer on Industry 4.0, conducted in partnership with Bpifrance and France Industrie). The main motivations cited are industrial performance (for 30% of respondents) and data control (27%). Note that ecological impact and energy performance were in third place this year (15%).
The Nexans Group took the first step towards change in late 2020, when it teamed up with Schneider Electric, a company with proven experience in transforming its own industrial base. The process initiated by Schneider Electric places the emphasis on reliability, productivity, improved availability through predictive maintenance, energy efficiency and protection against cyber-attacks. The first step in the partnership involved major investments at pilot sites in Autun, France and Grimsås, Sweden. The process will be deployed at eight more sites by the end of 2023, with the aim of upgrading all 45 Group plants on four continents by late 2025, at a pace of between 12 and 15 sites every year.
Nexans plants upgraded by the end of 2023
Nexans plants upgraded by late 2025
Nexans plants upgraded per year
These fundamental changes involve the mobilization of Group data: the raw material of this new industrial revolution. Although the proportion of data used by the Group rose from 5% to 10% between 2019 and 2023, the aim is to reach 70% by 2026.
“ We are approaching the Group's digital transformation on two levels, first by integrating new technologies into our operations, and second by creating a collaborative environment. ”
Vincent Dessale
Chief Operating Officer of NexansThis approach connects production tools using IoT and AI resources, while allowing employees to take back control through dashboards, decision-support indicators, and quality and safety monitoring. It also supports efforts to cut response time and time to market.
Reasons for a revolution: what actually changes in the field
First, we will see changes in the way we work every day. Because the transformation is not just about technology, even though connected machines, AI-powered robots are becoming an increasingly common site in factories, along with self-driving forklift trucks roving the aisles of the logistics centers by day and by night. However, the most spectacular changes concern human workers, with workshops packed full of screens, tablets and connected goggles.
This is a sensitive subject, since the success of the transformation will depend on how well people are able to work alongside machines. This is precisely the aim of Industry 5.0, as it is sometimes called. The objective is to expand and strengthen the digital transformation by supporting better collaboration between people and machines, while ensuring that creativity and well-being are not overlooked.
This aspect is taken into account from the outset in the Nexans project:
- Real-time dashboards monitor the smooth running of production lines, currently in each plant and soon across the Group's entire global industrial base. Real-time data supervision boosts industrial performance and quality control, while also reducing the consumption of energy and raw materials, and cutting energy costs by 15%.
“ We can now pick up on many errors before they occur. It’s a bit like being able to see into the future with all the data collected. ”
Tobias Karlsson
Predictive Maintenance Operator at Nexans in Grimsås, Sweden- A corporate social network gives operators access to video modules and tutorials, along with a chat forum. The forum is invaluable for discussing best practices and finding solution fast, since users are able to post questions directly for the online community. It is also a way to keep track of past actions, contributing to the sharing of information between operators, staff and management and the smooth running of day-to-day operations, while also helping workers to be more self-reliant.
“ When we get back from vacation, for example, all we have to do is look at the news feed to find out what's been happening while we've been away, on our line and on the site in general. ”
Mylène Iller
Production operator at Nexans in Autun, France- Connected goggles are used to reduce workplace stress, establishing a direct line between experts and operators at any time, to manage sensitive production phases or urgent production problems, through the use of augmented reality.
Lionel Fomperie, Nexans Group Industrial Strategy Director and Thomas Wagner, Nexans IS Performance Director give a general program overview and explain how Operations are working together with IT/OT to generate IT/OT and Cybersecurity platforms.
At this key stage in the process, the aim is for digitization to free operators from repetitive work, so that they can focus on tasks with higher added value. The digital transformation will also play a role in increasing the appeal of our business for the younger, digital-native generation, while creating opportunities for us to enrich job profiles, reduce the time spent on machines, and enhance skills through appropriate training programs.
To harness its full power, this new approach to managing the production base must be integrated with the company's strategic objectives. Taking this process as far as possible, Nexans is making sure that its industry 4.0 plan is consistent with the E3 management model, underpinning the transformation of the group by supporting the goals of economic performance, environmental virtue and employee commitment.
Lionel Fomperie, Group Industrial Strategy Director, Chao Li, Digital Development Engineer and Olivier Ameline, Nexans Excellence Way Director drive us through three use cases: Unified Operation Cockpit (UOC), MES Performance (Manufacturing Execution System) and SQDCE Digital board: S for Safety, Q for Quality, D for Delay, C for Cost & E for Environment.
Lionel Fomperie, Group Industrial Strategy Director, Chao Li, Digital Development Engineer and Olivier Ameline, Nexans Excellence Way Director drive us through three use cases: Unified Operation Cockpit (UOC), MES Performance (Manufacturing Execution System) and SQDCE Digital board: S for Safety, Q for Quality, D for Delay, C for Cost & E for Environment.
Our websites
Select your country to find our products and solutions
-
Africa
- Africa
- Ghana
- Ivory Coast
- Morocco
- North West Africa
- Americas
- Asia
- Europe
- Oceania