- Markets
- Catalog
- Services & Solutions
- Tools and Resources
- Downloads
- About Nexans
- Newsroom
-
Nexans Insights
- Nexans Insights
-
Blog Posts
- Overview
- The path to effective fire safety in buildings
- Big data & AI
- Electrical and Fire Safety
- IoT
- Unveiling innovations transforming the industry
- Transforming buildings industry with 3D printing and modular construction
- Powering the digital change
- Unleashing the power of DC buildings
- Sustainable buildings for a brighter future
- Industry 1, 2, 3, 4... and 5.0
- Nexans copper odyssey
- Localizador de tiendas
- Search
- Contact us
- Compare
- Sign in
Five innovations for buildings' revolution: Sustainable buildings for a brighter future
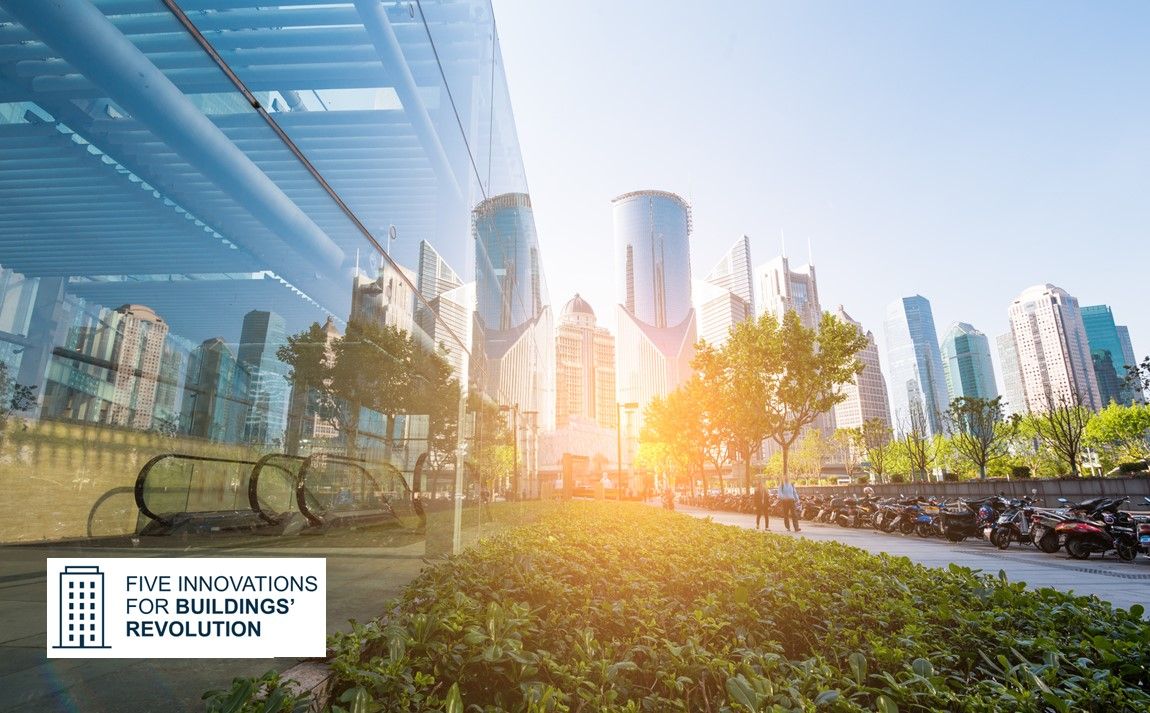
Today, governments from around the globe with bold commitments to reduce greenhouse gas (GHG) emissions are pressuring the construction and building sector to reduce its carbon emissions and consumption of raw materials.
And for good reason. Commercial and residential buildings are responsible for almost 40% of greenhouse gas emissions (GHG) and consume 30% of final energy globally. Decarbonizing the building and construction sector is critical to achieving net zero emissions by 2050. Doing so will need fundamental changes in how buildings are designed, built, and operated worldwide. This shift will require the sector to favor more environmentally friendly building materials and practices, institute better material efficiency strategies, and reduce raw material usage.
Innovative construction materials
The move to innovative low-carbon building materials is essential to reduce the building and construction sector's environmental impact. Concrete is not only the most commonly used building material but is responsible for 8% of global GHG emissions.
A viable alternative to traditional concrete is low-carbon brick made from recycled materials or traditional clay bricks fired in a low-carbon process using biogas from waste, biomass methanation, or solar and wind power.
Construction materials company Saint-Gobain, for example, is leading the way in the production of sustainable, low-carbon products. Earlier this year, the global company announced the production of zero-carbon plasterboard at its modernized plant in Fredrikstad, Norway. Decarbonizing the manufacturing process was possible by switching from natural gas to hydroelectric power, thus avoiding 23,000 tons of CO2 emissions annually. In addition, the company is the first in the industry to produce zero-carbon flat glass, made possible by using 100% recycled glass (cullet) and 100% green energy produced from biogas and decarbonized electricity.
Eco-friendly materials such as hemp and flax are viable alternatives for reducing the sector's environmental impact. Cavac Biomatériaux, specializing in the industrial application of plant fibers, manufactures insulation from hemp and flax.
Better material efficiency strategies
The 2022 Global Status Report for Buildings and Construction foresees global consumption of raw materials to double by 2060. By implementing better material efficiency strategies, there is a massive potential for the building sector to reduce its GHG emissions, according to the report's panel.
Furthermore, material efficiency strategies, including recycled materials, in G7 countries could reduce emissions in the material cycle of residential buildings by more than 80% in 2050. Globally, the Ellen MacArthur Foundation estimates that the circular economy would reduce CO2 emissions from building materials by 38% in 2050.
A key initiative within the European Union's Circular Economy Action Plan (CEAP) is the Digital Product Passport (DPP). This initiative aims to make sustainable products the norm in the EU by facilitating transparency throughout the value chain and boosting circular business models. Instituting a circular business model in the building and construction sector is key to reaching important sustainability targets.
Reducing raw materials usage
Construction materials and products are estimated to consume 50% of all raw materials extracted from the Earth's crust, and demolition activities represent 50% of all waste generated. To reduce its cables' environmental impact, Nexans increasingly uses low-impact materials throughout the production value chain.
It is projected that the availability of important raw materials will continue to decrease in the years to come. An example is copper, an essential component of electrical cables and wiring due to its high conductivity and strength. Because copper mining can no longer meet global demand, 40% of copper production comes from recycled copper.
For over 35 years, Nexans has been recycling copper and aluminum scrap as part of its Sustainable Development policy to reduce raw material usage and promote a circular business model. In 2008, Nexans and SUEZ launched RECYCÂBLES, France's leading recycler of cables and non-ferrous metals. The joint venture processes 36,000 tonnes annually of cables, generating 18,000 tonnes of metal granules and 13,000 tonnes of plastic. The combination of leading-edge technologies enables the generation of 99.9% pure copper granules.
Today, Nexans uses up to 15% of recycled copper in new cable manufactured and is on target to use recycled aluminum by 2024. Employing recycled copper, aluminum, and plastics provides Nexans' customers a sustainable product without compromising quality.
Environmentally friendly building materials
With the global floor area expected to double by 2060, implementing energy-efficient and environmentally friendly building materials and practices is vital.
Nexans is working to improve the impact of its products by sourcing components that meet reduced energy usage guidelines established by the company's Corporate Social Responsibility (CSR) directives. In addition, Nexans' R&D product development aims to protect the environment and human health by managing the chemical substances used in its manufacturing processes and ensuring that all new projects take into account the end product’s environmental footprint. For example, starting in 2025, a large part of cables manufactured at the Nexans facility in Autun, France, will be halogen-free to reduce their toxic gas emissions in the event of a fire.
Energy-efficient, zero-carbon buildings will require looking at how building materials are designed, made, and used. This will mean examining the value chain and changing how we make, use, and reuse all materials—from the actual product to the packaging and transportation—to reduce the industry's overall environmental impact.
Our websites
Select your country to find our products and solutions
-
Africa
- Africa
- Ghana
- Ivory Coast
- Morocco
- North West Africa
- Americas
- Asia
- Europe
- Oceania